The FIFO Method and How to Use It
The FIFO (first-in first-out) method is an inventory management strategy brands, retailers, private warehouses, and third-party logistics (3PL) providers can use when they deal with perishable goods or products that may become outdated or less useful over time.
This method ensures that the first products you purchase or create are the first to go out when customers place orders. By using older stock first, FIFO reduces the likelihood of inventory stagnation and minimizes holding costs.
FIFO is particularly effective in industries with rapidly changing product lifecycles or seasonal demand patterns because it helps businesses more effectively adapt to fluctuating market conditions.
According to a report in The Wall Street Journal, 55% of S&P 500 companies use FIFO as their primary inventory method. On the plus side, adopting the FIFO inventory valuation method can result in higher reported profits during inflationary periods created by lower costs of goods sold (COGS); however, because taxes are based on profits, it can also lead to increased tax bills.
What is the First-In First-Out (FIFO) method?
The first-in first-out (FIFO) method is an inventory management process based on the principle that your oldest inventory items are the first to use or sell. It's similar to how customers are served in a queue or line in a store based on their arrival order. This principle ensures a fair and orderly distribution of goods.
For retailers, FIFO offers several benefits. By giving priority to remaining inventory, you can more effectively manage the risk of perishable goods expiring or outdated products becoming obsolete. Maximizing resources can also lead to a reduction in waste and tangible cost savings with minimal losses. Additionally, FIFO can positively influence inventory management techniques and enhance storage space utilization for logistics providers that support these businesses.
FIFO can also help warehouse managers with inventory analysis for more accurate inventory records. By correlating real-time inventory with your most recent purchase orders, you can increase confidence that your inventory data is accurate and reflective of current stock levels, which can reduce the likelihood of stockouts or overstocking.
How to Calculate FIFO
Since inventory is an asset, it’s important to keep insight into your actual inventory values. FIFO can influence those numbers.
When using FIFO, always begin with the cost of your oldest items. If your purchasing amounts have gone up or down during your forecast period, you’ll need that data, too. Here's a formula to calculate cost of goods sold (COGS) based on FIFO:
COGS = Amount of Sold Inventory × Cost of Inventory
Here’s an example: You’re a retailer who sells video games. You purchase 50 video games at wholesale for $30 each, which gives you a beginning inventory value of $1,500.
Before you put the games on your shelves, the market predicts they will sell quickly, so you order 50 more. Unfortunately, the cost has increased to $35 per game, so your inventory value for the next 50 is $1,750. Now, your total inventory value is $3,250.
At the end of the first two weeks, you sell 45 games. Since you’re using FIFO and those 45 sold games were purchased at $30 each, your COGS is $1,350 (45 units x $30 per unit = $1,350).
You have five games left that you purchased for $30 each (5x30 = 150) and 50 games in stock valued at $35 each (50x35 = 1,750). Your ending inventory value is $1,900.
How to Use the FIFO Method
Implementing the FIFO method requires careful planning. Here are six steps retailers and 3PLs can take:
1. Organize Inventory with Accurate Labeling
If you manage a warehouse that is looking to implement a FIFO inventory management system, the first step you should take is to optimize your warehouse layout and inventory processes. This will facilitate inventory movement, picking, and packing based on product arrival dates. Also, consider arranging your stock storage locations to make older inventory items easily accessible to help your teams pick and dispatch those first goods. Fulfillment software tools–like warehouse management system (WMS) software–designed for inventory slotting optimization, slotting algorithms, and dynamic location assignments may also be beneficial.
Additionally, properly labeling and storing all of your inventory with identification markers such as batch numbers, expiration dates, or production dates is especially helpful for FIFO. Organizing your inventory systematically enables you to quickly locate items that have been in stock for a longer time and prioritize them for sale or use. You can simplify these processes with inventory and order fulfillment software to automate tasks like inventory tracking, label creation, and product categorization.
2. Track and Manage Inventory
To keep track of the movement and usage of inventory within your warehouses, implement robust inventory tracking and management processes. You can use advanced fulfillment software with inventory management functions like real-time inventory and order tracking, batch tracking, and product management to gain visibility into your inventory levels. This can help you track the age of stock and ensure FIFO compliance. To minimize errors and improve overall inventory accuracy, use tools like barcode scanning and RFID tagging for accurate inventory identification and tracking.
3. Train Your Employees
To ensure the effectiveness of your FIFO processes, it is crucial to have well-trained inventory and order fulfillment employees. Educate your employees and provide comprehensive training about the importance of FIFO, along with the specific implementation and management procedures relevant to their roles. Establish actionable and repeatable processes so your team can accurately and quickly identify older inventory items, understand expiration dates, and prioritize shipping based on FIFO standards. You can use fulfillment software to assign and track FIFO-related tasks, while workflow automation can streamline training processes and ensure consistency for FIFO implementation.
4. Conduct Routine Inventory Audits
To ensure your FIFO processes function effectively, conduct regular audits and inventory inspections. You can start by inspecting your shelves, checking expiration dates, and verifying inventory records. Consider using inventory management software to streamline the audit processes and get real-time visibility into inventory and order levels. This will help you create automated audit reports and identify issues that need more attention.
5. Use Data Analytics and Demand Forecasting Tools
By using data collection, analytics, and inventory demand forecasting tools available within fulfillment software, you can accurately predict future inventory requirements and collaborate with suppliers to ensure you always have the right quantity and current products available. Leveraging demand forecasting capabilities, you can gain insight into your changing inventory needs while also minimizing excess stock issues and obsolescence problems. Adopting a proactive FIFO approach supported by technologies and automation tools can help you enhance overall supply chain efficiency, resulting in improved customer satisfaction and cost savings.
6. Collaborate and Communicate
For FIFO success, you need effective collaboration and communication strategies–not just with your employees, but also with suppliers across your supply chain. This can help ensure timely inventory delivery and accurate product documentation. You should also create clear communication channels with your suppliers about FIFO requirements and expectations. Fulfillment software with supplier management capabilities can help you and stakeholders track supplier performance, monitor delivery schedules, and communicate effectively. Additionally, demand forecasting and inventory planning tools can help you plan for future inventory needs and coordinate replenishment to maintain optimal inventory levels.
The Benefits of Using FIFO
Consider using FIFO based on its benefits and whether or not your business handles perishable goods, products with expiration dates, or rapid product turnover.
- Reduce waste by ensuring you use or sell older inventory first. This will decrease the worry that your goods will expire or become obsolete before use. Prioritizing the sale of older items can minimize inventory write-offs and maximize inventory value.
- Optimize inventory turnover by ensuring you process older inventory and ship it out first. This minimizes the risk of inventory obsolescence and product quality by rotating inventory based on arrival times while improving warehouse efficiency. It also reduces the need for extra storage space and inventory holding costs.
- Increase customer satisfaction by prioritizing order fulfillment for older orders, ensuring no one gets unusable products when they need them. Ensuring customers receive products with longer shelf lives reduces the likelihood of returns or complaints, enhances customer satisfaction, and can enhance your brand’s reputation for product quality and reliability.
- Get greater visibility into inventory levels and supply chain movement so you can more effectively track inventory aging, identify slow-moving items, and make data-driven decisions to optimize inventory management.
- Get more accurate financial reporting and balance sheets by matching revenue with actual cost of goods sold. This ensures that profitability metrics accurately reflect the true cost of your inventory so you can make more informed pricing and strategic decisions.
When to Consider Other Inventory Methods
While the FIFO method has many benefits, it’s not without disadvantages.
One disadvantage of using FIFO is the increased risk of inventory obsolescence, especially if you manage rapidly changing or seasonal products. This is because FIFO prioritizes the sale of older inventory items before newer ones, which could lead to potential losses if more in-demand products don't sell.
Implementing FIFO can also be complex, requiring meticulous inventory tracking and management procedures that can be resource-intensive. Warehouse managers must ensure accurate inventory labeling and tracking, implement effective inventory storage solutions, and ensure staff rotates inventory based on receiving dates. As the size of your operations and inventory management increases, implementing FIFO gets harder.
Also, if your business has fluctuating demand patterns or seasonal flow of goods, you may find FIFO less effective. When demand for newer inventory items is higher than older ones, FIFO may result in excess inventory of older items, which creates inventory buildup and increases inventory holding costs. In these instances, flexible inventory management strategies that can adapt to evolving demand patterns may be better options
And, in some cases, FIFO could actually decrease profit margins, especially during inflation or when inventory costs increase.
Retailers and 3PLs should consider alternative inventory methods in certain situations, especially when dealing with highly specialized or customized products as using FIFO may lead to excess inventory and other inefficiencies. In such cases, you may want to explore other options such as the LIFO method (last-in first-out) and average cost methods.
However, LIFO inventory management may not be the best choice for managing perishable goods or items with limited shelf life. Although it may provide income tax benefits by reducing profits, it's not suitable for all situations. And, while the average cost inventory management method simplifies accounting standards by tallying the average cost of all units of a specific inventory type, it may not accurately represent your actual profitability, especially when prices fluctuate or inventory quality varies.
Determining which stock management method best suits your business depends on several factors. To determine if FIFO is the right choice for you, assess your inventory characteristics, understand customer demands and industry standards, and review your operational requirements and goals. Consider factors such as product shelf life, inventory turnover rates, and storage capacity. Conducting a cost-benefit analysis and comparing FIFO with alternative inventory systems can also help determine which method is best for your specific needs.
If you’re unsure if FIFO is right for you, consider partnering with supply chain professionals or consulting with industry experts who can help you make the best decisions based on their expertise and your specific needs and goals.
Start Managing Your Inventory with Extensiv
Whether you’re using FIFO, LIFO, accurate cost, or some other inventory management method, Extensiv can help you streamline and optimize inventory management, warehousing, and shipping processes.
With advanced inventory tracking and visibility, demand forecasting and planning, order fulfillment optimization, and seamless integration capabilities with your entire fulfillment technology ecosystem, you can continuously optimize inventory management, increase your bottom line, and improve customer satisfaction.
By design, Extensiv’s platform of software solutions can help your warehouse teams accurately allocate inventory against orders by automatically applying FIFO principles when new orders come in. For example, using its inventory management tool, you can view which orders are committed/allocated against a particular SKU and/or warehouse.
Extensiv also enables real-time visibility into inventory levels and product aging, facilitating FIFO adoption. With dedicated barcode scanning features, you can also ensure accurate, real-time inventory and order tracking, timely inventory rotation, and fewer human errors with decreased time-consuming manual tasks.
Interested in learning more? Request a demo today!
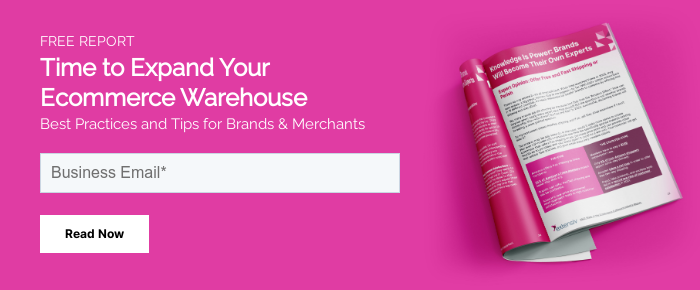
-
You’ll read about:
Be the first to know
Subscribe to our newsletter